Understanding the Importance of **Instrument Fitting** in Modern Industries
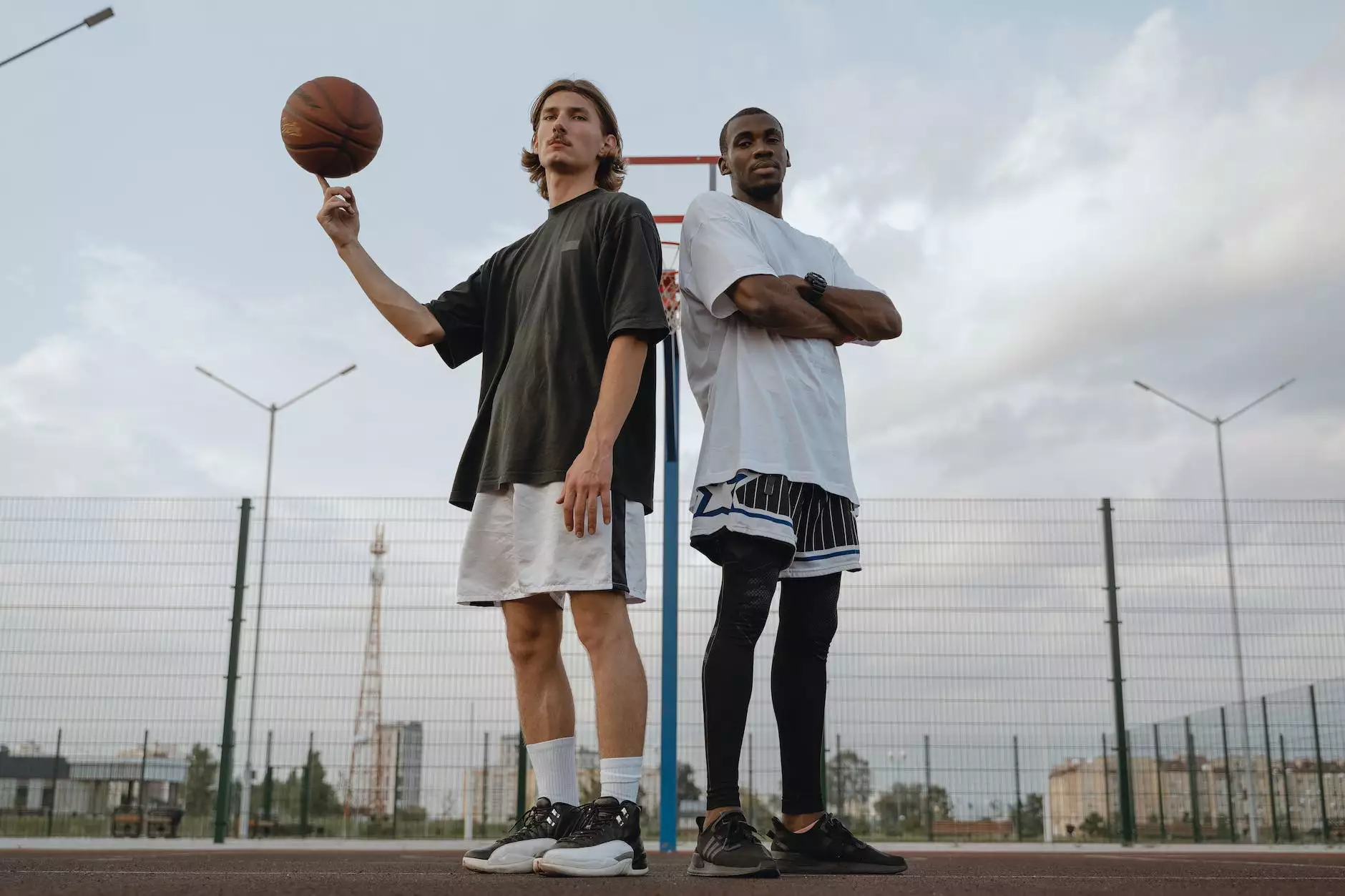
In today's competitive business landscape, the quality and accuracy of components play a crucial role in ensuring operational success. One such critical aspect is instrument fitting, a field dedicated to the precise assembly and integration of devices and tools across various sectors. This article delves deep into the significance of instrument fittings, their applications, benefits, and what makes them indispensable in modern industry.
What is Instrument Fitting?
Instrument fitting refers to the practice of accurately connecting and installing various instruments and tools used in different industrial applications. These fittings ensure that instruments such as gauges, valves, sensors, and piping connections work together seamlessly to maintain system integrity and performance. The process of fitting these instruments requires attention to detail, engineering knowledge, and a thorough understanding of the materials involved.
The Critical Role of Instrument Fitting
In many sectors, such as manufacturing, energy, healthcare, and aerospace, the need for precision cannot be overstated. Here are some of the critical roles that instrument fitting plays:
- Ensuring accuracy: Proper fittings are essential for accurate measurements and readings, which are crucial in data-driven decision-making.
- Enhancing efficiency: Well-fitted instruments can help streamline operations, reducing downtime and increasing productivity.
- Maintaining safety: In industries like oil and gas, improper fittings can lead to catastrophic failures. Good fittings guarantee system safety and operational reliability.
The Process of Instrument Fitting
The process of instrument fitting typically involves several stages, each requiring careful planning and execution. Here’s an overview of the steps involved:
1. Assessment and Planning
Before any fitting can take place, a comprehensive assessment of the instruments and systems involved is essential. This phase includes:
- Analyzing the requirements of the specific application.
- Understanding the environmental conditions where the fittings will be used.
- Determining compatibility among the various instruments.
2. Selection of Materials
The choice of materials is vital in achieving successful instrument fittings. Materials must be selected based on:
- Corrosion resistance.
- Temperature and pressure ratings.
- Compliance with industry standards and regulations.
3. Installation
Once the materials are selected, the actual installation can begin. This stage involves:
- Careful alignment of instruments to avoid mechanical stress.
- Tightening fittings to the recommended torque specifications.
- Testing for leaks and ensuring proper operation of the assembly.
4. Maintenance and Inspection
After installation, regular inspection and maintenance are necessary to ensure that everything is functioning correctly. This process includes:
- Routine checks for wear and tear.
- Calibration of instruments to maintain accuracy.
- Immediate attention to any signs of failure or malfunction.
Applications of Instrument Fitting
Instrument fitting is crucial across multiple industries, each with its unique requirements. Here are some notable applications:
1. Manufacturing
In manufacturing, precision is essential for producing high-quality products. Instrument fittings are used in measuring devices, control systems, and machinery, ensuring that operations are carried out efficiently and safely.
2. Oil and Gas
The oil and gas industry relies heavily on instrument fittings to manage and monitor the extraction and transportation of resources. Proper fittings ensure safety and efficiency, as well as compliance with stringent regulations.
3. Healthcare
In healthcare, instruments must be fitted with extreme precision to guarantee functionality. Devices such as blood pressure monitors, infusion pumps, and surgical instruments require reliable fittings to maintain their integrity and ensure patient safety.
4. Aerospace
The aerospace industry demands the highest levels of accuracy and safety. Instrument fittings in aircraft and spacecraft are critical for navigation systems, engine controls, and communication devices, where failure is not an option.
The Benefits of High-Quality Instrument Fittings
Investing in high-quality instrument fittings offers numerous benefits that extend well beyond initial costs:
1. Improved Performance
High-quality fittings ensure that instruments perform at their best. Accurate readings and reliable operation lead to better decision-making and enhanced productivity.
2. Cost Efficiency
While the upfront costs of quality fittings may be higher, the long-term savings through reduced maintenance costs and operational downtime can be significant.
3. Enhanced Safety
Proper fittings play a crucial role in maintaining safety standards. They help prevent leaks, failures, and accidents that could lead to severe repercussions in high-risk industries.
4. Compliance with Regulations
Many industries have stringent regulatory requirements that demand the highest standards of materials and fittings. Sourcing proper instrument fittings ensures compliance with these regulations, avoiding legal and financial penalties.
Choosing the Right Supplier for Instrument Fittings
When it comes to procuring instrument fittings, selecting a reputable supplier is essential. Here are some factors to consider:
1. Quality Standards
Ensure that the supplier adheres to international quality standards, such as ISO certifications, to guarantee the reliability of their products.
2. Range of Products
A good supplier offers a comprehensive range of fittings compatible with various instruments. This variety enables businesses to find the exact fittings they need for their applications.
3. Technical Support
Look for suppliers that provide technical support and guidance. This assistance can be invaluable for installation, maintenance, and troubleshooting.
4. Customer Reviews and Reputation
Research customer reviews and industry reputation to gauge the reliability and performance of the supplier's products.
Conclusion: The Future of Instrument Fitting
The landscape of instrument fitting is constantly evolving with advancements in technology and materials. As industries strive for greater efficiency, safety, and accuracy, the demand for superior instrument fittings will only increase. Businesses must stay ahead by continuously improving their fitting practices and investing in quality components.
At fitsch.cn, we specialize in providing top-quality instrument fittings and unparalleled support to ensure your operations are safe, efficient, and compliant with the highest standards. Explore our offerings in the fittings for sale category today and see how we can help enhance your industrial processes.