Understanding Die Casting: A Comprehensive Guide to Die Casting Die Manufacturers
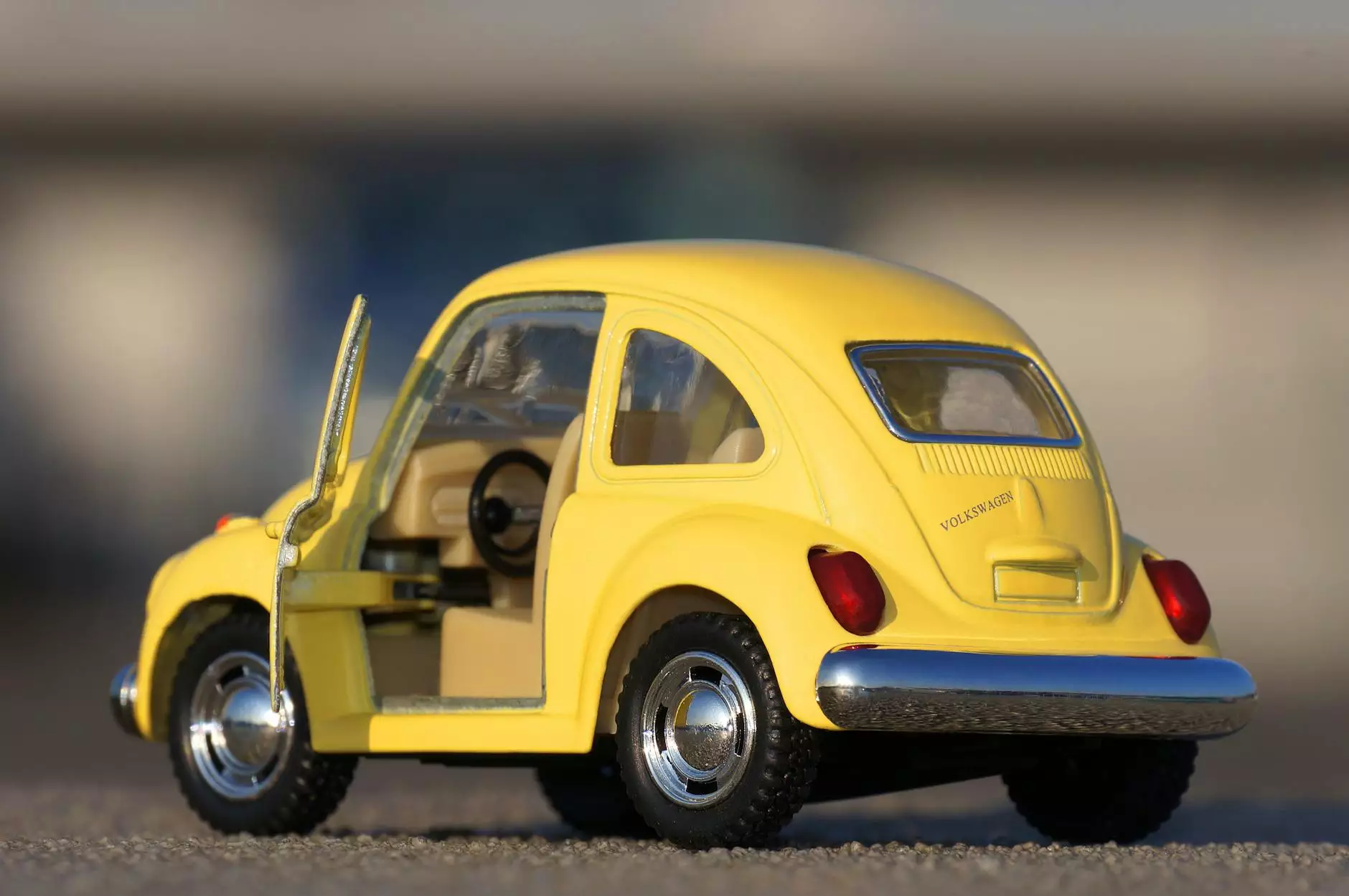
In the manufacturing realm, the term die casting die manufacturers resonates significantly among industries looking for efficiency and precision. This article aims to provide an in-depth exploration of die casting, the role of die casting die manufacturers, and their impact on the metal fabrication landscape. From the intricacies of the die casting process to the benefits of selecting top-tier manufacturers, we cover it all in comprehensive detail.
What is Die Casting?
Die casting is a versatile manufacturing process used to produce metal parts by forcing molten metal into a mold cavity under high pressure. This method is typically employed with non-ferrous metals such as aluminum, zinc, and magnesium. The die casting process has several critical advantages:
- Cost-effectiveness: Once the initial die is created, large production runs become economically viable.
- High precision: Die casting allows for intricate shapes and tight tolerances.
- Excellent surface finish: Parts produced through die casting typically have a smooth surface, requiring less post-processing.
- Rapid production rates: The process allows for high-volume production without compromising quality.
The Die Casting Process Explained
The die casting process can be broken down into several key steps:
- Creating the Die: The die is a metallic mold designed to create a specific shape. It is manufactured to high tolerances to ensure accurate parts.
- Heating the Die: Before pouring molten metal, the die is usually heated to improve the flow characteristics of the metal.
- Injecting the Molten Metal: The molten metal is injected into the die at high pressure, filling the mold cavity quickly. This step is critical as it determines the quality of the final part.
- Cooling and Solidifying: After the injection, the metal cools and solidifies within the die.
- Removing the Casting: Once cooled, the die is opened, and the casting is ejected.
- Finishing Touches: Various finishing processes may be required, including trimming, machining, or surface treatments.
The Role of Die Casting Die Manufacturers
Die casting die manufacturers play a pivotal role in ensuring the success of die casting operations. They are responsible for designing and producing the dies used in manufacturing processes. Selecting a reliable and high-quality die casting die manufacturer can significantly impact the outcome of a project. Here are some factors to consider:
1. Quality of the Dies
The quality of the die is paramount in the die casting process. High-quality dies lead to improved casting quality, reduced defects, and lower recycling costs. A reputable die casting die manufacturer uses high-grade materials and advanced technologies to produce durable and precise dies.
2. Customization Options
Every project is unique, requiring tailored solutions. An adept die casting die manufacturer should offer customization options to meet specific project requirements. Whether it's unique shapes, sizes, or materials, the ability to customize dies can elevate product quality and performance.
3. Advanced Technology
Technological advancements have revolutionized die casting processes. Manufacturers who utilize cutting-edge technology, such as computer-aided design (CAD) and computer-aided manufacturing (CAM), can ensure higher precision and faster turnaround times. This also allows for better troubleshooting and modifications during the die design phase.
4. Experience and Expertise
Experience is invaluable in manufacturing. A die casting die manufacturer with years of industry experience is likely to understand the nuances of die design and production. Their expertise allows for more efficient problem-solving and innovation.
5. Customer Support and Services
Excellent customer service is crucial when selecting die casting die manufacturers. They should offer support throughout the manufacturing process, from initial design discussions to post-production services. This support builds a relationship of trust and ensures that any issues are promptly addressed.
Key Benefits of Partnering with Leading Die Casting Die Manufacturers
Partnering with established and reputable die casting die manufacturers offers numerous benefits that can enhance production efficiency and product quality. Here are some noteworthy advantages:
- Consistency in Quality: Leading manufacturers maintain rigorous quality control processes, ensuring that each die produced meets the expected standards.
- Reduced Lead Times: With efficient production practices, top manufacturers can significantly reduce lead times, enabling quicker project completions.
- Innovative Solutions: Partnerships with skilled manufacturers can introduce innovative techniques and practices that improve overall production workflows.
- Cost Savings: By investing in high-quality dies from reliable manufacturers, businesses can save on production costs associated with defects and rework.
Trends in the Die Casting Industry
The die casting industry is continuously evolving, driven by technological advancements and changing consumer demands. Here are some current trends shaping this sector:
1. Eco-Friendly Practices
Increasing environmental awareness has led many die casting die manufacturers to adopt sustainable practices. These may include using recyclable materials, energy-efficient production processes, and reducing waste during manufacturing.
2. Automation and Robotics
The integration of automation and robotics in die casting is streamlining production, increasing precision, and reducing labor costs. Automated processes contribute to consistency and safety in manufacturing environments.
3. Light Weighting
With the growing demand for lightweight components, particularly in the automotive and aerospace industries, die casting die manufacturers are focusing on producing lighter materials without compromising strength. This trend is pushing innovation in alloy composition and die design.
4. Digital Prototyping
Digital prototyping, facilitated by computer simulation software, allows manufacturers to visualize and test designs before production. This capability reduces the risk of errors and accelerates the development of new products.
Choosing the Right Die Casting Die Manufacturer
With numerous options available, choosing the right die casting die manufacturer is crucial for the success of your project. Here are some steps to consider when making your decision:
1. Research and Compare
Start by researching potential die casting die manufacturers. Look for those with a strong reputation and positive reviews. Compare their offerings, technologies, and capabilities. Websites like deepmould.net can provide valuable insights.
2. Assess Capabilities
Evaluate each manufacturer’s capabilities regarding the materials they work with, their production capacity, and customization options. Ensure they can meet your specific project requirements.
3. Request Samples
Don’t hesitate to request samples or case studies showcasing their previous work. This will give you a tangible sense of the quality and craftsmanship you can expect.
4. Ask About Quality Control Processes
Inquire about the manufacturer's quality control processes. A robust quality assurance system will ensure that the dies produced meet strict standards, leading to superior final products.
5. Evaluate Communication and Support
Effective communication is key in any partnership. Assess how responsive and supportive the manufacturer is during the initial discussions. This can be a strong indicator of their customer service throughout the project.
Conclusion
Understanding the role of die casting die manufacturers is essential for businesses looking to maximize the efficiency and quality of their manufacturing processes. The die casting process, characterized by its precision and cost-effectiveness, offers significant advantages to various industries. By partnering with the right manufacturer, companies can benefit from high-quality dies, innovative solutions, and a dedicated support system. As the industry continues to evolve, staying informed about trends and best practices will be crucial for those seeking to thrive in the competitive landscape of metal fabrication.
In summary, choosing the right die casting die manufacturer can lead to remarkable improvements in productivity, quality, and overall project success. Whether you are an engineer, a product designer, or a business owner, investing the time to find a reputable partner will pay dividends in the long run.